Otomobillerde karbon fiber malzemeyle artık daha sık karşılaşıyoruz
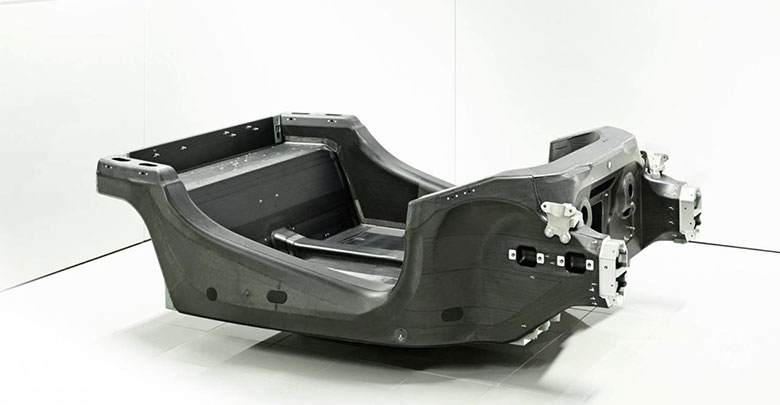
Bir zamanlar sadece belli başlı modellerde kullanılan karbon fiber yapıları artık daha sık görmeye başladık
Bir zamanlar süper otomobil üreticilerinin sadece en güçlü modellerinde kendine yer bulan karbon fiberin artık günümüzde daha yaygın kullanılmaya başlandığına şahit oluyoruz.
Motor sporları dışında, düzenli olarak karbon fiber takviyeli plastik (CRFP) yapıların kullanıcıları arasında bir zamanlar McLaren, BMW ve Lamborghini gibi markalar vardı. İtalyan firma 2010 yılında Aventador’un monokok şasisini şirket içinde üretebilmek adına “RTM-Lambo” adı verilen yeni bir üretim şekline sahip bir fabrika kurdu.
RTM (reçine transfer kalıplama) yönteminde, özel üretilmiş olan takviye malzemeleri kalıp içine yerleştirilir. Kalıplar kapatılır. Ve malzemeye basınçlı olarak reçine enjekte edilir. Böylelikle yüksek kaliteli gövde parçaları çok daha düşük maliyetlerle elde edilebilir.
Lamborghini modellerinde de karbon fiber malzeme kullanılıyor
Aventador‘un gövdesinin üst yarısı ‘prepreg’ yöntemiyle kullanılarak hazırlanmış ve kısmen sertleştirilmiş. Önceden reçine emdirilmiş karbon fiber malzemelerin daha sonra şekillerinin bozulmaması için soğuk ortamlarda saklanmasına pre-impregnated yani prepreg ismi verilmiş. Prepreg, parlak A Sınıfı cilalı bileşenleri yapmanın en iyi yoludur, ancak pahalıdır. Bu nedenle gövdenin alt yarısı RTM-Lambo kullanılarak yapılır. RTM-Lambo’nun standart RTM’den farkı ise genel hatları elde etmek için uygulamadan önceden çok az miktarda reçine eklenmesidir. Son olarak, üst ve alt bileşenler büyük bir kalıpta birbirine bastırılır, emprenye edilir ve monokok şasinin tamamlanması için sertleştirilir.
McLaren, 2010’da piyasaya tekrar döndüğünde dünyanın en büyük CRFP üretim otomobil monokok şasileri siparişini Salzburg firması Carbo Tech’e verdi. Lamborghini’nin yaklaşımından farklı olarak, McLaren’in Monocells’i 35 ton ağırlığındaki çelik kalıplarda basit RTM kullanılarak yapılmış. Amaç, süreci hızlandırmak değil, şasiden elde edilebilecek en yüksek performansı almaktı. Yine de, her bir şasi efsane McLaren F1’den 10 kat daha hızlı yapıldı. Şimdi, McLaren, ilk defa Mart ayında McLaren Üretim Merkezi’ne teslimat yapan, Monocells and Monocages üreten 50 milyon £’lık İnovasyon Merkezi’ne sahip.
Karbon fiberin yaygınlaşmasının önündeki en büyük engel maliyeti
Seri üretim modellerinde karbon fiberin yaygınlaşmasının önündeki engel ise maliyeti, çünkü karmaşık yapıların imalatı hala insan eli ile yapılıyor. Üretim ve işlem maliyetleri, toplam bileşen maliyetinin% 33 ila 75’ini oluşturuyor.
BMW modellerindeki “Carbon Core” ise kalıbın içine karbonla birlikte yerleştirilmiş çelik bileşenlere sahip hibrit bir tasarımdan oluşuyor. Bir seri üretim otomobilde CRFP kaportaya sahip olmaya en yakın model BMW i3. Ancak bu yapının mevcut modelden sonra kullanılmasına devam edilmeyebileceği de gelen haberler arasında.
Tüm bunlara rağmen maliyet azaltma konusunda adımlar atılmaya devam ediyor. Voith Composites, CRFP’nin arka panel ve Audi A8’in pandizotu için için Voith Roving Aplikatör adı verilen otomatik bir sistem geliştirdi ve bunu “kompozit dünyasında çığır açan bir teknoloji” olarak nitelendiriyor. Ancak şimdilik, alüminyum, seri üretim otomobiller için favori olmaya devam ediyor ve daha sürdürülebilir, geri dönüşüm için% 95 daha az enerji harcıyor.